 |
 |
 |
 |

ВЫПЛАВКА АЛЮМИНИЕВЫХ СПЛАВОВ В ДУГОВЫХ ПЕЧАХ ПОСТОЯННОГО ТОКА НОВОГО ПОКОЛЕНИЯ
В. А. Зыскин, СИ. Поздняков (ОАО СМК), B.C. Малиновский, канд. техн. наук (000 НТФ «ЭКТА»)
Production of Aluminium Alloys in Electric Arc Constant Current Furnaces of New Generation. V.A. Zyskin, S.I. Pozdnyakov, V.S. Malinovsky.
The quality of AK7K alloy produced in DPPTU-0,5 AG electric arc constant current furnace is studied. It is shown that high purity metal, content of hydrogen being no more than 0.23 cm3/100 g, is produced. The unique feature of melting in the electric arc constant current furnace is rather deep removal of hydrogen and nonmetallic inclusions during charge melting.
Законы рынка диктуют необходимость создания новых видов продукции, способной конкурировать не только внутри нашей страны, но и с иностранными фирмами.
Одним из путей решения данной проблемы явилось строительство в ОАО СМК нового цеха по производству литых автомобильных колес с использованием самого современного оборудования - дуговых печей постоянного тока нового поколения, разработанных специалистами НТФ «ЭКТА».
В качестве способа литья было выбрано литье под низким давлением, основными преимуществами которого являются выход годного не менее 90 %, повышенная плотность отливок и современный уровень автоматизации процесса.
В конце 2002 г. была установлена первая группа машин и началась опытная отливка автомобильных колес из алюминиевого сплава на основе АК7пч. Номинальная вместимость миксера LPT 600 машины литья под низким давлением (МЛНД) составляет 500 кг. Выплавку проводили в тигельных электропечах сопротивления САТ-0,25. Производительность этих печей составляет 16 кг/ч при расходе электроэнергии 34 кВт-ч. Для обеспечения производственной программы в ОАО СМК использовали четыре печи САТ-0,25.
Основные преимущества печей сопротивления - это получение металла достаточно высокого качества и сравнительно высокий коэффициент полезного действия. Однако эти печи имеют низкую производительность и трудны в эксплуатации, что связано с частым выходом из строя нагревательных элементов. Использование таких печей не позволяет механизировать процессы загрузки и приготовления расплава.
Анализ возможностей современных плавильных агрегатов привел к решению: установить в ОАО СМК универсальные дуговые печи постоянного тока нового поколения (ДППТНП) в агрегатном исполнении (ДППТУ-0,5АГ), разработанные и поставляемые НТФ «ЭКТА», для плавки стали, чугуна и сплавов на основе алюминия, меди, никеля и кобальта.
Печь ДППТУ-0,5АГ представляет собой две плавильные емкости, подключенные к одному источнику электропитания. Производительность этих печей 800 кг/ч (в 50 раз выше, чем у CAT) с расходом электроэнергии при работе в одну смену 512 кВт-ч. Это в 2,8 раза ниже, чем при выплавке в CAT. Основные технические данные ДППТУ-0.5АГ для плавки алюминиевых сплавов приведены в табл. 1.
Согласно концепции НТФ «ЭКТА» печь оснащена системой магнитогидродинамического перемешивания расплава и в ней реализованы специальные режимы плавления.
В ОАО СМК освоена выплавка в печи ДППТУ-0,5АГ алюминиевого сплава АК7К и алюминиевой лигатуры алюминий-марганец, планируется плавить лигатуры на основе алюминия, ферросплавы, а также освоить технологию переплава шлака и стружки.
Основной задачей данной работы является освоение нового метода плавки в печи ДППТУ-0,5АГ с целью получения отливок высокого качества при минимальных издержках производства.
Таблица 1
Технические характеристики электропечи ДППТУ-0,5
|
Параметр
|
Значение |
номинальное |
допустимое |
фактическое, в
соответствии с
технологическим процессом |
Номинальная вместимость (по алюминию), т |
0,5 |
0,6 |
0,6 |
Установленная мощность электропечи, кВА |
840-890 |
|
600 |
Время расплавления, мин, не более |
20 |
|
45* |
Удельный расход электроэнергии на расплавление, кВт-ч/т |
320 |
340 |
640* |
Диаметр графитизированного электрода, мм |
100 |
— |
100 |
Расход графитизированного электрода, кг/т, не более |
1,2 |
|
4* |
Угар шихты. %, не более |
1,5 |
— |
0,5 |
* Данные для полного цикла плавки с затратами на расплавление и технологические процессы. |
Проведено сравнение показателей при производстве алюминиевого литья с использованием печей САТ-0,25 и ДППТУ-0,5АГ при выпуске автомобильных колес в МЛНД. В количественном отношении составы
шихты при плавках в печах САТ-0,25 и ДППТУ-0,5АГ были близки (табл. 2).
Специальные методы удаления водорода и неметаллических включений в процессе плавления и внепечной обработки не применялись, так как их удаление обеспечивалось термодиффузией водорода при расплавлении и МГД-перемешивании расплава. Содержание водорода в сплаве составляло 0,12 см3/100 г и не превышало 0,23 см3/100 г.
При плавке в электропечах ДППТУ-0,5АГ была применена технология «холодного легирования». Из выплавленного металла отливал и автомобильные колеса в МЛНД. Химический состав литых автомобильных колес из сплава АК7К приведен в табл. 3.
Для выплавки лигатуры алюминий-марганец в печи ДППТУ-0,5АГ в качестве шихтовых материалов применяли отходы сплава АД1 и марганец Мн997. Для рафинирования использовали стандартный рафинирующий флюс. Лигатуру разливали в изложницы высотой 50 мм с помощью разливочного ковша. Состав лигатуры дан в табл. 4.
Макроструктуру колес исследовали в поперечном направлении и оценивали на соответствие утвержденным эталонам допустимой и недопустимой макроструктуры литых автомобильных колес из сплава АК7К. Макроструктура колес плавок, полученных в электропечах САТ-0,25 и ДППТУ-0,5АГ, достаточно плотная и однородная с незначительной пористостью, соответствует эталону № 3 - допустимой структуре
Таблица 2
Сравнительный состав шихтовых материалов
|
САТ-0,25 |
ДППТУ-0,5 |
Силумин АК12оч Алюминий А7 Медь МООк Магний Мг90 Лигатура алюминий- титан-бор Отходы сплавов АД0 и АД1
Технологические отходы сплава АК7К |
Силумин АК12оч Алюминий А7 Медь МООк Магний Мг90 Лигатура алюминий- титан-бор Отходы из сплавов АДО и АД1
Технологические отходы сплава АК7К |
— |
Кремний металлический КрО (плавки №645, 646) |
Флюсы: Degasai ALT 200 «Дегазал», Eutektal Alt 200 «Эвтектал», Mikrosal ALT 100 «Микросал» фирмы Шайфер |
Проводили работу по подбору рафинирующих флюсов |
Таблица 3
Химический состав литых автомобильных колес из сплава АК7К
|
Нормативный документ |
Основные элементы, % маc. |
Примеси, % маc., не более |
Cu |
Mg |
Si |
Ti |
Мп |
Fe |
Zn |
ТУ1-801-9002-2004 ТКП150-001-2004* |
0,5-0,8 0,3-0,5 |
0,25-0,4 0,3-0,4 |
6,0-8,0 7,0-8,0 |
0,08-0,15 0,10-0,15 |
0,3 0,02 |
0,3 0,3 |
0,5 0,015 |
* Внутрицеховой регламент по химическому составу. |
Таблица 4
Химический состав лигатуры алюминий-марганец, % маc.
|
Нормативный документ |
Mn |
Si |
Cu |
Mg |
Fe |
Ni |
Zn |
Ti |
Протокол химического состава
По техническим указаниям 150-004-2004 |
10,0 8-12 |
0,1 0,5 |
0,024 0,2 |
0,03 0,1 |
0,4 0,8 |
- 0,1 |
0,02 0,2 |
0,01 0,1 |
Механические свойства и микроструктура литых автомобильных колес в закаленном состоянии |
Тип печи |
Номер плавки |
Зона вырезки |
σв' МПа |
σ0,2' МПа |
δ, % |
HB, МПа |
Размер колоний эвтектики, мкм |
Размер кремнийсодержащих частиц, мкм |
Размер усадочных пор, мкм |
ДППТУ-0,5 |
643 |
Спица |
222,1 227,9 220,2 |
142,3 146,2 144,2 |
9,7 11 12,7 |
76,3 |
167х46 |
от 2,0 до 6,7 |
Длина 73,7-254,5; ширина 47-147,7 |
Толстая закраина |
230,2 244 229,2 |
154,5 143,2 148,1 |
13 11,7 12,7 |
72,4 |
ДППТУ-0,5 |
645 |
Спица |
237,6 228,1 236,8 |
146,6 149,6 149,6 |
10 8,3 10 |
76,3 |
134х93,8 |
Мелкодисперсные |
Длина 67,0-113,9; ширина 26,8-73,7 |
Толстая закраина |
232,7 247,4 240 |
151,6 151,1 144,9 |
6,7 8,3 10,7 |
70,6 |
САТ-0,25 |
560 |
Спица |
222,2 221,4 233,9 |
141,1 126,5 142,1 |
7,7 8,3 8 |
70,6 |
- |
от 4,2 до 92,4 |
Длина 21-137,3; ширина 7-37,4 |
Толстая закраина |
21,9 220,4 218,7 |
151,1 134 144,6 |
7,3 8,3 7,3 |
70,6 |
САТ-0,25 |
569 |
Спица |
230,2 237,3 226,6 |
140,6 154 148,7 |
8,3 9,7 6,7 |
72,4 |
- |
от 2,1 до 71,4 |
Длина 27,3-144,1; ширина 14,7-92,5 |
Толстая закраина |
234,6 228,4 237,2 |
147,1 137,1 140,6 |
10 9 9 |
72,4 |
литых автомобильных колес. На макротемплетах литых колес дефектов в виде шлаковых и других включений, трещин не обнаружено. Размер зерен на макротемплетах колес находится в пределах от 0,05 мм (на границах отливок) до 0,2 мм (в центре отливок).
В табл. 5 приведены результаты микроструктурного анализа литых автомобильных колес из сплава АК7К, выплавленного в печах ДППТУ-0,5 и САТ-0,25, в закаленном состоянии.
По результатам микроанализа лигатуры алюминий-марганец установлено, что микроструктура лигатуры алюминий-марганец однородная, микропористая с размерами частиц основной фазы А16Мп от 30 до 200 мкм.
Механические свойства литых колес опытных плавок определяли при комнатной температуре в состоянии поставки после термической обработки Т4 (Тзак=535±5 °С, τвыд=4 ч, Тводы=40 °С)
Образцы вырезали из трех зон спица, толстая закраина (по 3 образца) и обод (по два образца).
Усредненные показатели механических свойств литых автомобильных колес типоразмера 7Jx16CH из сплава АК7К представлены на гистограмме (см. рисунок).
Оценку чистоты металла плавок № 643, 645 (электропечь ДППТУ-0,5) и плавок № 58, 61 (электропечь САТ-0,25) из сплава АК7К проводили методом технологической пробы. Этот метод основан на выявлении дефектов в виде отдельных (гладких) площадок в изломах горячедеформированных образцов. Образцы испытывали после горячей деформации с 4- и 5-кратной осадкой. Качество металла оценивали по результатам определения отношения площади дефектов (плен, мм2), обнаруженных в изломах технологических проб, к общей площади исследуемого излома (см2) по формуле
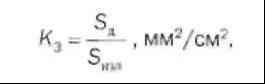
гдеКз - коэффициент загрязненности; Бд - площадь дефектов, мм2, SM3n - площадь излома, см2.
Коэффициент загрязненности дефектами (окисными пленами) в плавке № 643 имеет одинаковый уровень: Кз=0,47 мм2/см2, в плавке № 645 Кз=0,97 мм2/см2 (ДППТУ); в плавке № 58 Кз=4,91 мм2/см2 и в № 61 К3=3,89 мм2/см2 (САТ-0,25). Коэффициент загрязненности для плавок № 58, 61 (CAT) достаточно высокий. Обработка расплава аргоном в плавках № 58 и 61 не дала положительного результата.
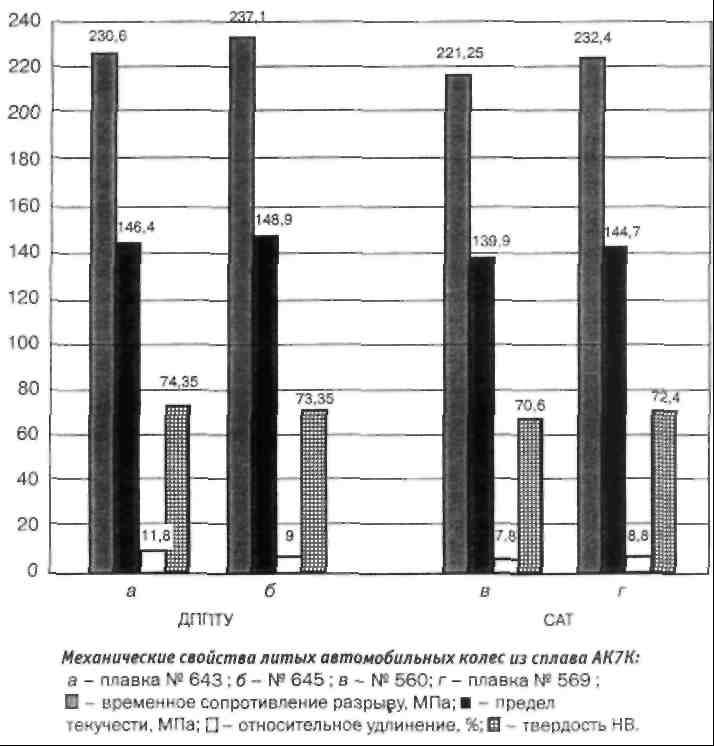
Выводы
1. Сравнение результатов исследуемых плавок показало, что в печи ДППТУ-0,5АГ выплавляется металл высокой чистоты.
2. При плавлении металла в печи обеспечивается высокая чистота металла, а при длительной разливке (примерно от 1 до 4 ч), качество поддерживается преимущественно средствами рафинирования.
3. Качество металла повышается при обработке расплава флюсами в оптимальном количественном соотношении.
4. Исследования на газонасыщенность показали содержание водорода в сплаве не более 0,23 см3/100 г.
5. При плавке в электропечах ДППТУ-0,5 можно проводить «подмораживание» расплава. В результате, кроме рафинирования расплава, достигается измельчение эвтектических составляющих (типичная плавка № 645). Общее время плавки при этом увеличивается в первой плавке (холодная печь) до 10 мин и в последующих плавках до 5 мин (горячая печь).
6. В электропечи ДППТУ-0,5 возможно применение новых технологий по выплавке алюминиевых сплавов, лигатур и ферросплавов.
7. В электропечи ДППТУ-0,5 можно осуществлять переплав отходов металлургического производства (шлака, съемов, стружки и т.д.).
8. При соблюдении технологического процесса по выплавке сплавов в печи ДППТУ-0,5 угар металла не превышает 1,5%. При плавке плотно загруженной шихты угар составляет 0,5%.
9. Повышенный расход электроэнергии и графитовых электродов, а также работа на пониженной мощности связаны (в случае применения ДППТУ-0,5) с длительными простоями печи, вызванными низкой производительностью машины литья под низким давлением (МЛНД).
10. Применение электропечи ДППТУ-0,5 обеспечивает автоматизацию процесса плавки, быструю загрузку шихтовыми материалами.
11. Уникальной особенностью процесса плавки в печи ДППТУ-0,5 является достаточно глубокое удаление водорода и неметаллических включений в процессе плавления шихты.
|
 |
 |
|